Application Guide
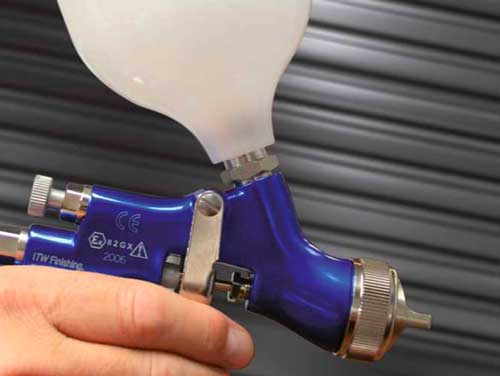
Related Posts
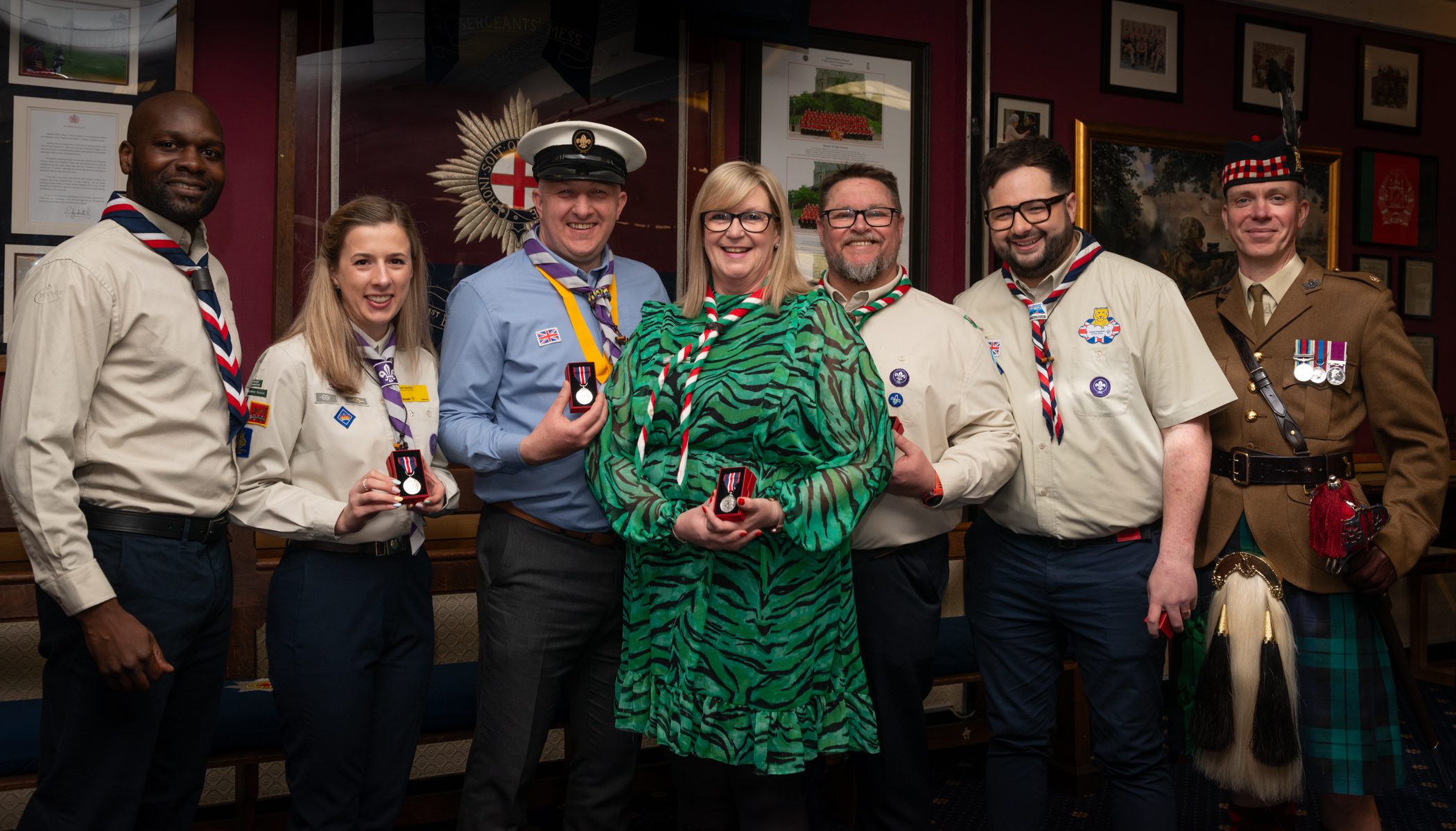
Congratulations Kris Hennegan As He Receives National Honour for Supporting the Coronation of HM King Charles III
Congratulations Kris Hennegan As He Receives National Honour for Supporting the Coronation of HM King Charles III
Continue Reading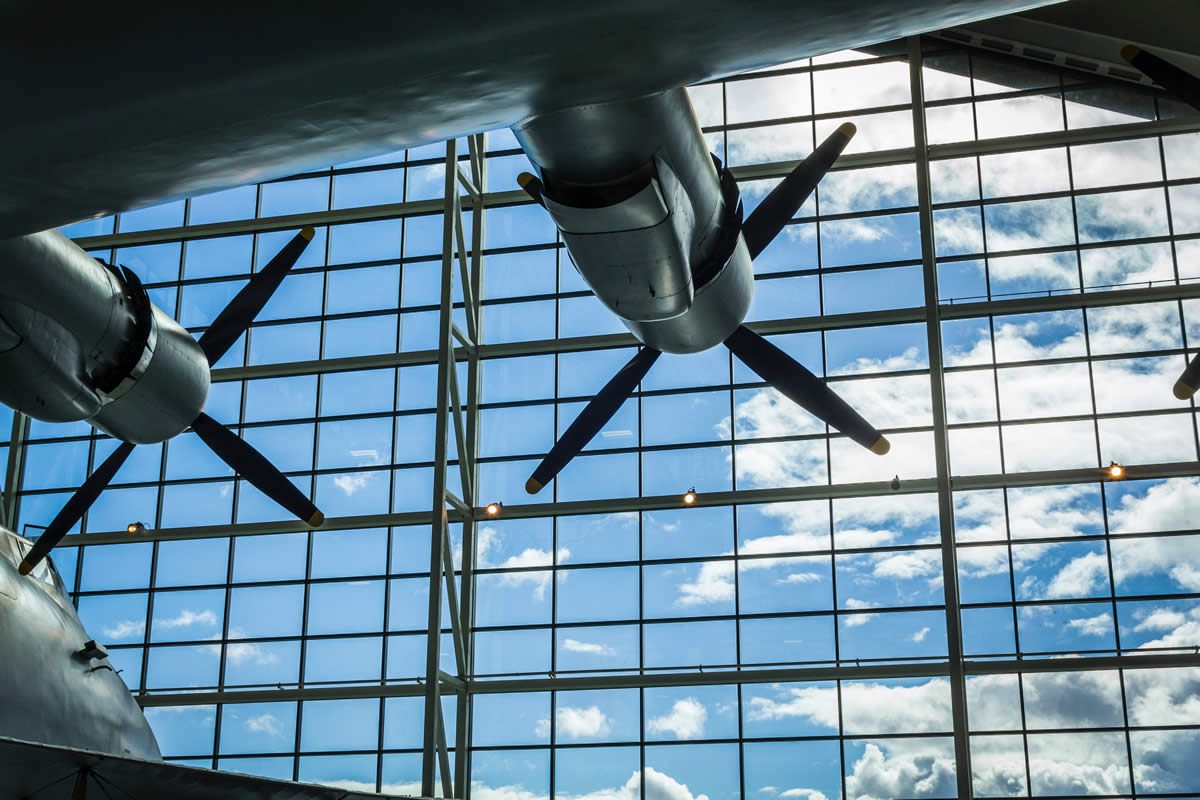
Excellence in the Skies: Aerospace Coating Performance Metrics with Indestructible Paint
Excellence in the Skies: Aerospace Coating Performance Metrics with Indestructible Paint
Continue Reading